Limometal
- PRODUCT CATEGORY
Company digitalisation
- DATE
2019
- DURATION
4 Months
About
Limometal is mass production and export tinsmith company. Company used spreadsheets and conventional techniques to keep track of all the orders, material tracking, receipt outputs and old vector tools for tin sketching needed for production crew. They wanted to digitalise the whole system in a single webapp.
As the only designer on the team, I worked closely with the founder, mechanical engineers to conceptualize the entire product that aligns with the new direction, vision and technical requirements. My role involved product direction, wireframing concepts, laying out the information architecture, UX, visual design, and prototyping. The objective of the 4-month project was to digitalise the whole process and test it out with all employee groups (accountats, production, mechanical engineers).
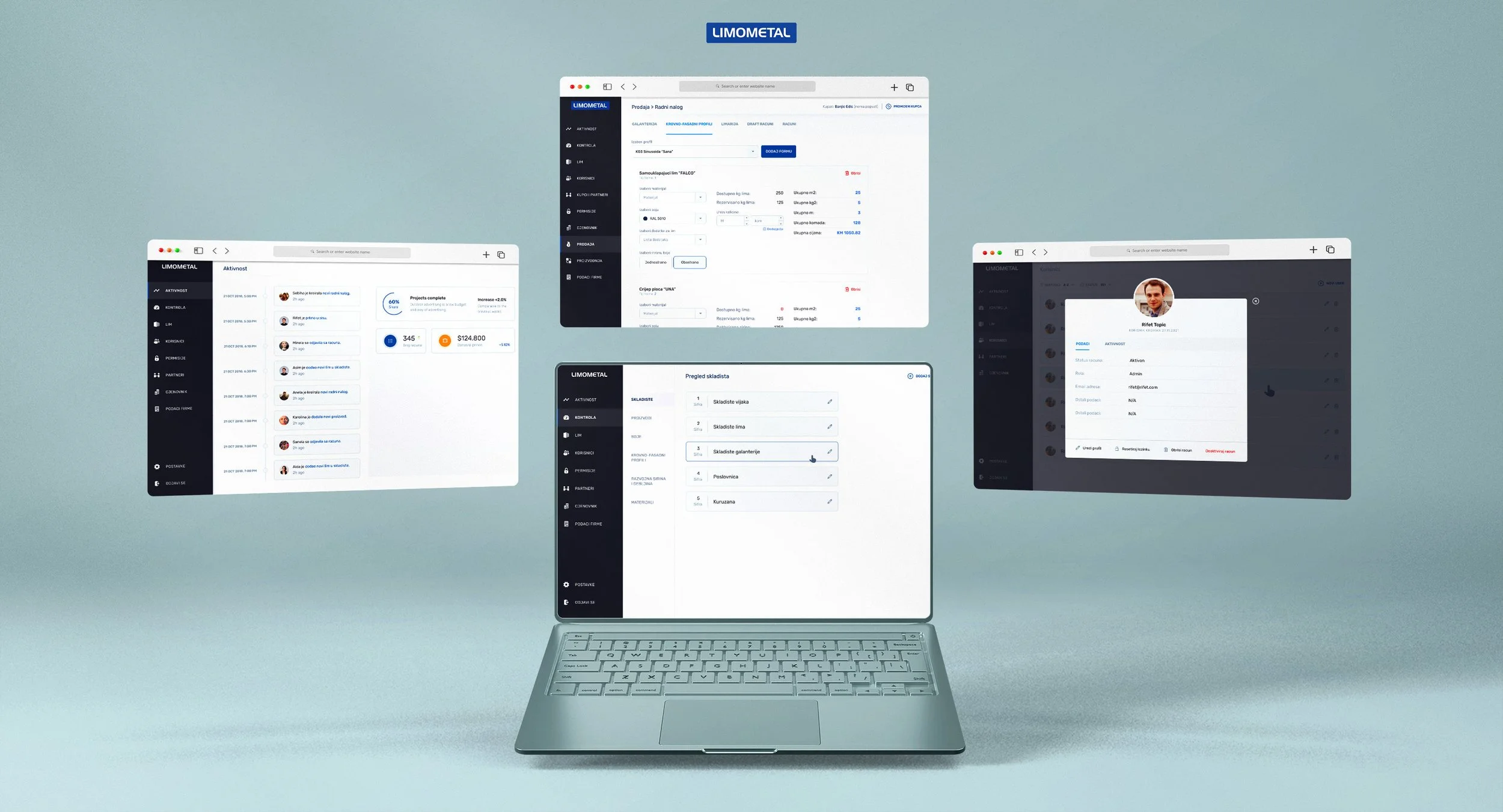
Planning the roadmap
What we knew from the initial meeting brief with the founders is that this is going to be highly technical product, meaning lot’s of tables, custom tool integrations and sensitive financial control. Crucial part was getting the information architecture right. Due to this product being done in controlled number of users, we had all the access needed for direct research with end users.
Plan was as follows (in order):
gather all the specification requirements from engineers and finance department
set the timeline and business goals with founders
conduct user interviews with actual employees and to be end users
set up sitemaps
ideate - wireframe possible solutions
adapt the existing ui guidelines to most essential component list (no time for actual design system)
high fidelity work
usability testing with users and apply the feedbacks
Information architecture
The product as a whole was functionally divided into 3 flows:
Admin
Sales
Production
Challenges
· Giving admin all options to control the flow of information and control to users
· Making an intuitive flow for exporting customer orders
· Sending the order to production
After discussion with company holders, it was decided that production crew should be distributed with tablets, and due to the nature of work environment, all orders will be accepted through responsive tablet apps.
*due to sensitive information, I was asked not to present this part of the app
User interview insights
· Extensive searching options should be implemented due to sheer number of data
· Temporarily saving receipts for future confirmation when customers are indecisive
· One page scannability - due to nature of business, accountants are creating the receipts while discussing the options with the customers
· Production controls should be as simple as Accepting the order and updating the status of it
Exploring design treatments
Admin
Presented below is the control panel for general overview and managment of all material, inventories, color and subsets needed for a production of customized tins.
User overview and Permission controls
Overview of sortable tin materials and all associated material specification connected to various tin distributors.
Finance
Product preparation flow & receipt summary
Light & Dark theme
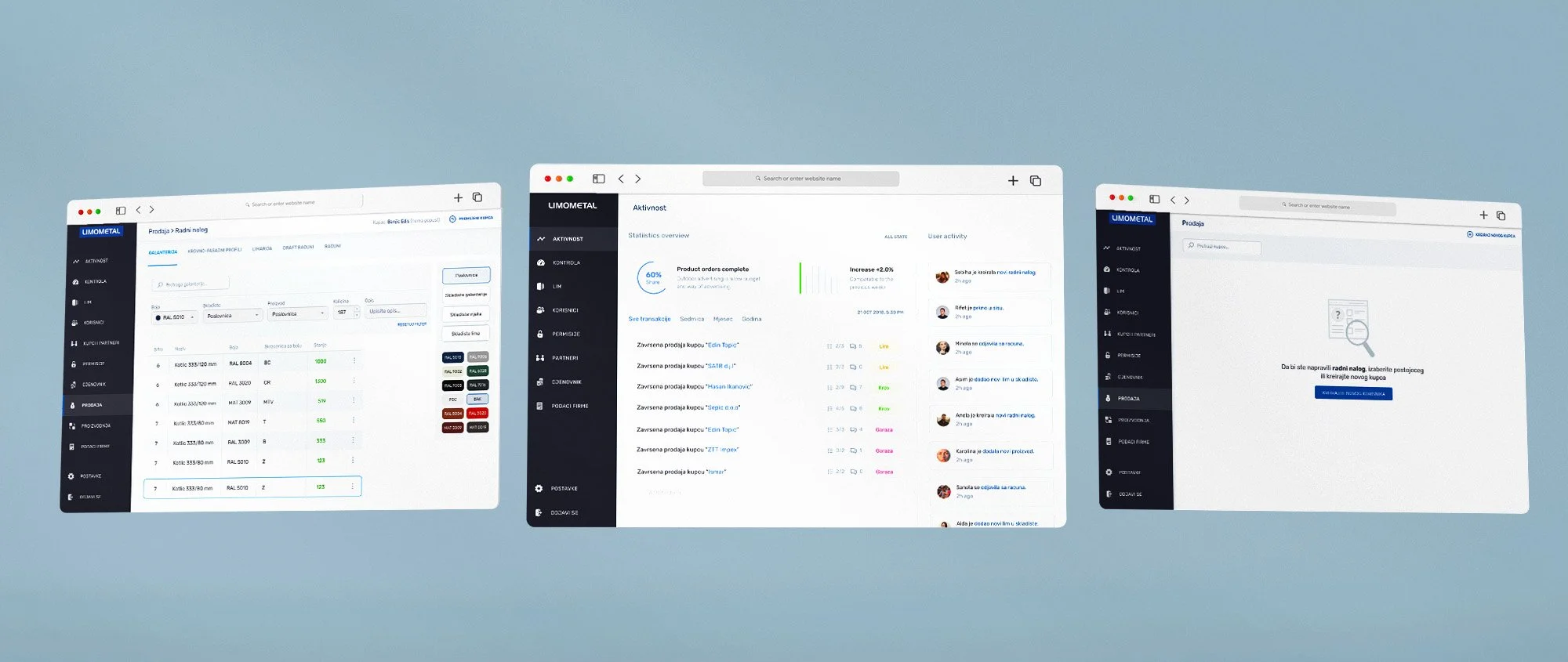
Usability testing insights
We did a live testing with employees and production crew and we learned:
a number of older employees had a problem with legibility of text (text was small, especially in data heavy tables)
period of adaptation was needed in setting up the product flow due to controls being different then the ones that the employees were used to - we applied “Law of locality” and grouped all the controls to the areas which they affect
admin crew found it cumbersome to implement data from old spreadsheets to the new database but this was inevitable to full transfer to the digitalised product
What we learned
This was a “technically” complex project mostly due to the huge diversity of materials and their dimension involved into creating a single product. I’m really happy with the decision of going with tablets for the production crew as it made their workflow much easier and provided instant feedback and overlook to the management team.
I would say the biggest problem was actually understanding the nature of business for this specific company and all the engineer complexities that come with it. Nevertheless, we were in constant communication with the founders and engineer trying to figure out how to transform the stone-age process they had into simplief modern solution.
In the end we:
made it easier for management to track whats happening in the financial and production segment
connected all the areas of the company into a single hub
modernized and simplified the overview of all customers and their previous/ongoing transactions
simplified the workflow from finance to production
implemented statistics section for the founders